News & Updates
New: Kitting / Bundling / Manufacturing
September 24, 2019
Today we’re thrilled to announce the addition of Kitting and Bundling. This powerful new feature enables you to use existing inventory to create new assembled products.
What Are Kits & Bundles Used For?
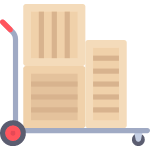
Anytime you want to combine inventory into a single product for sale you can now assemble it and sell it as a whole (instead of selling all the pieces individually). This is especially useful for manufacturing new products from parts, creating bundled deals, or even combining smaller units into a larger unit of measure (ie. 10 pieces assembled into 1 box).
Note: Different industries may refer to this kitting functionality with a wide range of different terms such as manufacturing, assemblies, packaging, etc. We’re sticking with Kitting & Bundling for simplicity’s sake.
How Kitting & Bundling Works
- You create a Kit Template.
- You assemble new units from the Kit Template to replenish its stock.
- The pieces used to assemble the newly assembled units are deducted.
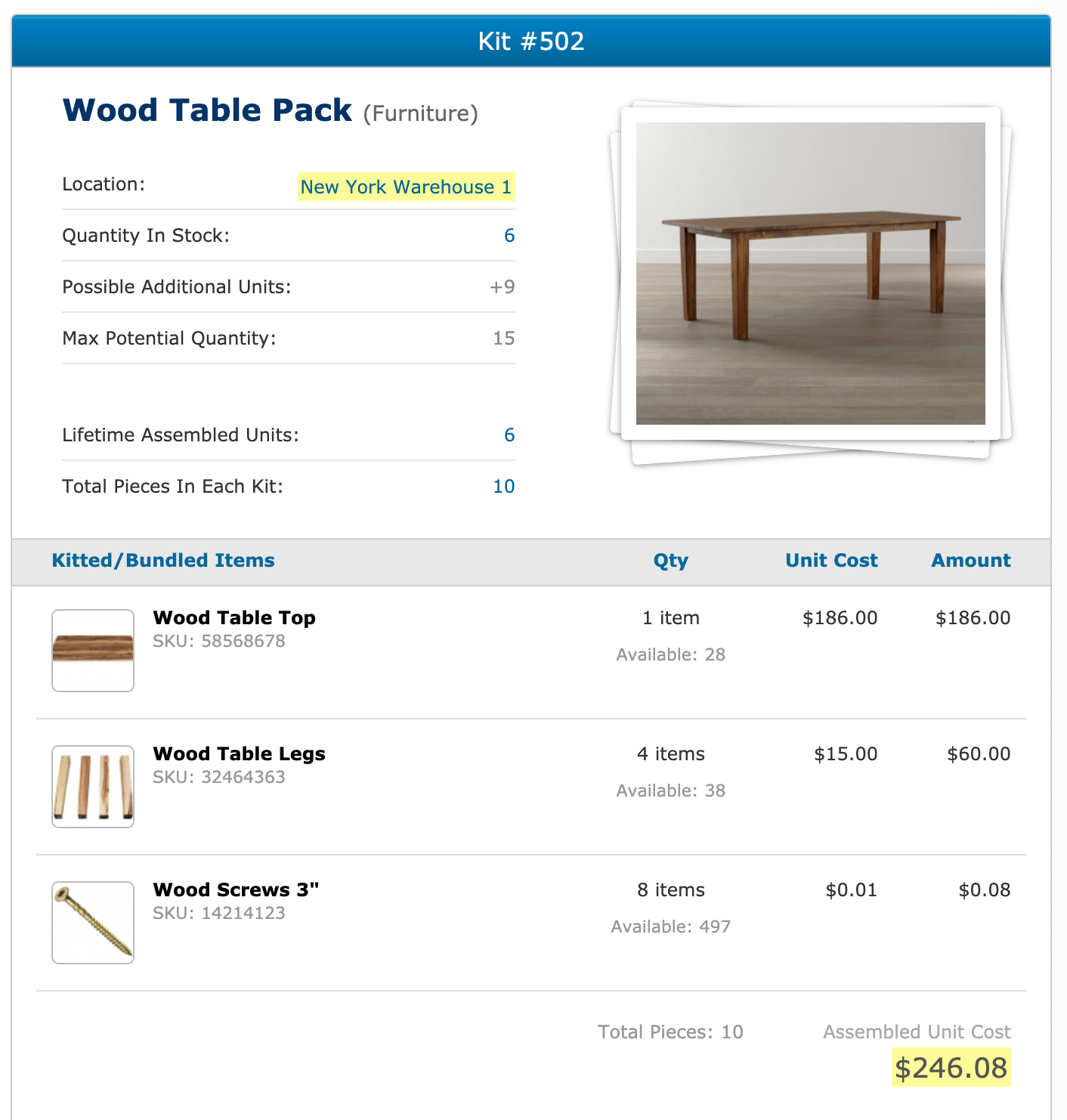
Creating a Kit Template
Creating Kit Templates is essentially like outlining the recipe of what needs to go into this new kit. You can add as many items as you like and specify any quantity needed to complete the kit. Once you have a Kit Template saved, it creates a new inventory item just like any other item in your inventory list with a few differences. Mainly, this item cannot be added to Purchase Orders for replenishment since you’re assembling them yourself – so you have to “Assemble” them to replenish their stock levels.
Assembling New Units From a Kit Template
When you’re looking to assemble more units for a kit you can quickly reference some valuable calculations. Based on the kit template we can determine what the maximum amount of new quantities can be for the item based on how much quantity is in stock for all the pieces in your kit as well as based on the location you’re selecting. Combining this calculation with what you already have in stock, SalesBinder can tell you your Maximum Potential Quantity for any kit in any location. You cannot assemble more units than what you have in physical stock.
If you have multiple inventory locations setup you have to select which location you’re assembling the stock in, and then you get to specify how many new units you’re going to assemble there. If you have enough stock to assemble those units, it will successfully save those assemblies in the kitted item’s “Assembly List” so you can see how many units were assembled on any given day and by who. You can also undo assembling items from the assembly list if you need to take them apart again.
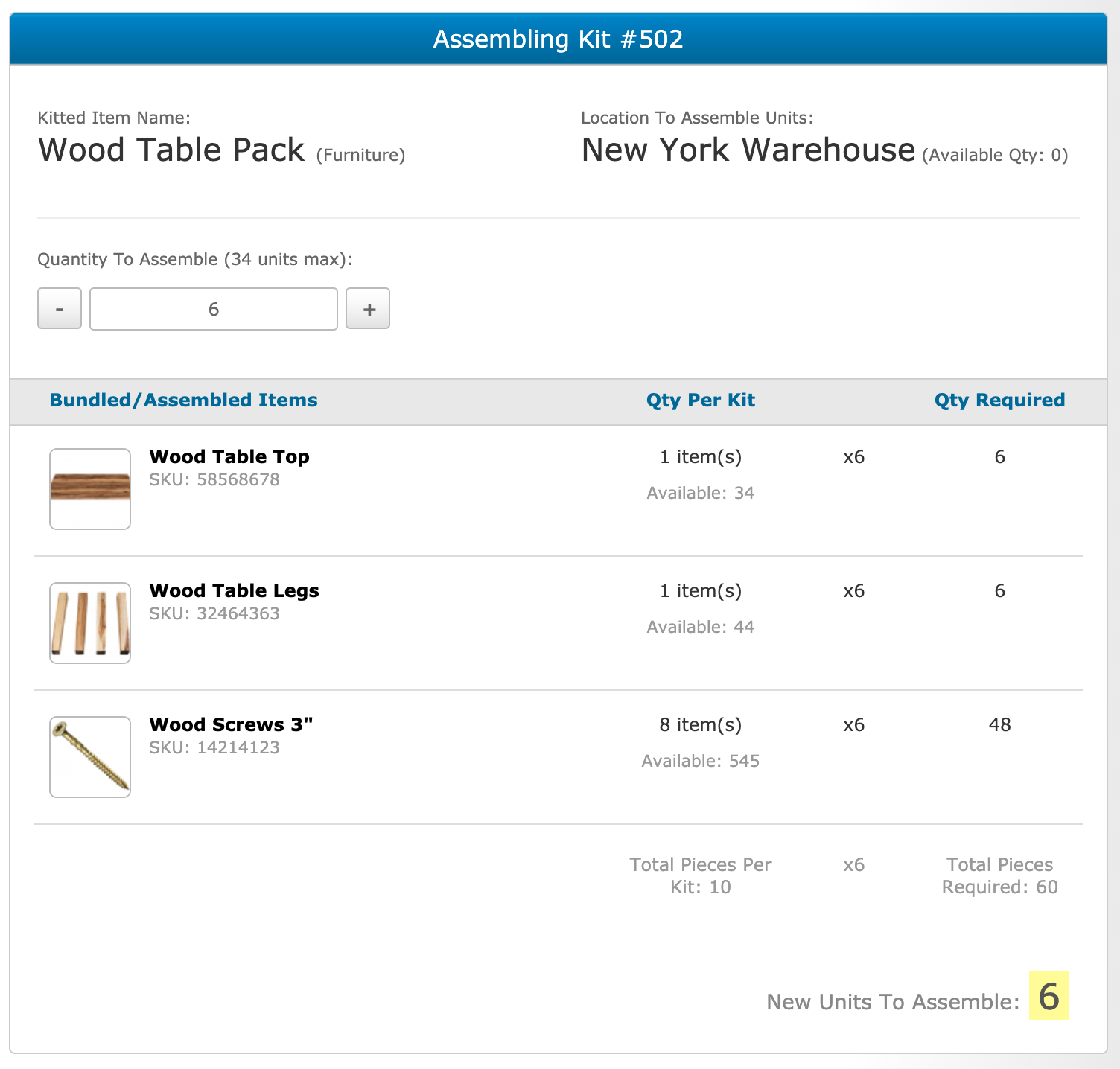
What Happens When a Kit is Assembled
When you successfully assemble new units, SalesBinder will automatically deduct all the pieces required to assemble the total amount of new units you specified, as well as replenish the assembled inventory item’s quantity with those newly assembled units.
It only requires a couple clicks to assemble new units, however, a lot of things have to happen in the background; such as verifying quantities available, checking for low inventory to send reminders, updating activity feeds, and logging all changes in quantities in each item’s quantity ledger.
In addition to all of those things happening in the background, we also have to check if all of the items within the kit have had their unit costs change. If the assembled kit now has a different assembled unit cost due to changing supplier prices, we apply a weighted average cost calculation to the new assembled units merging with any existing assembled units to keep your inventory valuation accurate.
What Else Can Kits & Bundles Do?
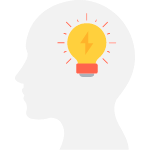
In addition to now being able to assemble new units from your available inventory, we wanted to take this to the next level so we also worked really hard to support nesting kits within kits. Here’s a basic example:
If you were assembling a coffee table, you could create a kit for a 4-pack of table legs + 4 screws, then add that kitted 4-pack into a new kit with a table top to complete your coffee table kit. Your coffee table kit would contain two items, the table top, and the pre-assembled 4-pack of legs & screws.
The benefit to creating kits within kits in this example is that it would allow you to order table legs in single units from your supplier, then package them into 4-packs (or 3-packs) when you receive them, then create completed coffee tables with different style table tops and reuse the assembled packs of table legs in other similar kits.
You can actually go many levels deeper within nesting kits (ie. a kit within a kit within a kit, etc). Currently our automated calculations for displaying your maximum possible quantities only goes 1 level deep but we’ll be adding support to recursively go through each nested kit in the next couple of weeks so you’ll be able to see how many possible units you can create no matter how many deeply nested kits are within a kit.
Selling Assembled Kitted Items
Since a kitted item in SalesBinder is treated exactly the same as any other inventory item, you can add kitted items to your estimates and invoices just like anything else. They’ll only display the assembled kitted item details as a single line-item (not all the miscellaneous pieces). You can set your own pricing and item descriptions as well.
How To Get Started
We’re offering this new powerful functionality to everyone and it’s available right now. You can try it out and see how powerful it is over the next few weeks and then we’ll be offering this to all paid subscription plans as a $9/mo add-on going forward.
As always, if you have any feedback on this new update or anything else, we’d love to hear it!
– The SalesBinder Team –
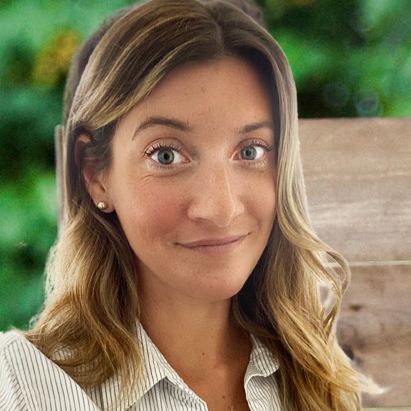